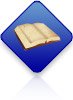
Technical Articles From Seamark zm Tech Group
Read technical articles about electronics manufacturing added by Seamark zm Tech Group
- SMTnet
- »
- Technical Library
- »
- Contributors
- »
- Articles from Seamark zm Tech Group
0 technical article added by Seamark zm Tech Group
Company Information:
NO RESULTS
Seamark zm Tech Group has no technical articles posted yet.