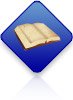
Technical Articles From ASM Assembly Systems (DEK)
Read technical articles about electronics manufacturing added by ASM Assembly Systems (DEK)
- SMTnet
- »
- Technical Library
- »
- Contributors
- »
- Articles from ASM Assembly Systems (DEK)
7 technical articles added by ASM Assembly Systems (DEK)
Company Information:
Stencil Printing Process Tools for Miniaturisation and High Yield Processing
Jun 12, 2023 | Clive Ashmore & Mark Whitmore
The SMT print process is now very mature and well understood. However as consumers continually push for new electronic products, with increased functionality and smaller form factor, the boundaries of the whole assembly process are continually being challenged. Miniaturisation raises a number of issues for the stencil printing process. How small can we print? What are the tightest pitches? Can we print small deposits next too large for high mix technology assemblies? How closely can we place components for high density products? ...And then on top of this, how can we satisfy some of the cost pressures through the whole supply chain and improve yield in the production process! Today we are operating close to the limits of the stencil printing process. The area ratio rule (the relationship between stencil aperture opening and aperture surface area) fundamentally dictates what can and cannot be achieved in a print process. For next generation components and assembly processes these established rules need to be broken! New stencil printing techniques are becoming available which address some of these challenges. Active squeegees have been shown to push area ratio limits to new boundaries, permitting printing for next generation 0.3CSP technology. Results also indicate there are potential yield benefits for today's leading edge components as well. Stencil coatings are also showing promise. In tests performed to date it is becoming apparent that certain coatings can provide higher yield processing by extending the number of prints that can be performed in-between stencil cleans during a print process. Preliminary test results relating to the stencil coating technology and how they impact miniaturisation and high yield processing will be presented....
NanoClear Coated Stencils
May 22, 2023 | DEK Engineered Products
Our customers' issues • Apertures are getting smaller • Paste does not release as well • Contaminates the bottom of the stencil • Increases defects / reduces yield Insufficient solder Bridging Solder balls on surface of PCB Flux residue • Requires more frequent cleaning • Reduced efficiency (wasted time) • Increased use of consumables (cost) USC fabric (use "cheap" fabric to reduce cost) Lint creates more defects Cleaning chemistries (use IPA to reduce cost) IPA breaks down flux and can create more defects...
Investigating the Metric 0201 Assembly Process
Dec 24, 2020 | Clive Ashmore
The advance in technology and its relentless development is delivering yet another surface mount assembly challenge. To meet the market demand for products with higher functionality whilst reducing the overall product size, the next generation of chip package is being readied upon the surface mount community. The Metric 0201 will have dimensions in the order of 0.25mm x 0.125mm, as a result the entire assembly process will be questioned as to its ability to deliver high volume/quality product....
Screen and Stencil Printing Processes for Wafer Backside Coating
Sep 09, 2009 | Mark Whitmore, Jeff Schake.
Stencil printing equipment has traditionally been used in the surface mount assembly industry for solder paste printing. In recent years the flexibility of the tool has been exploited for a wide range of materials and processes to aid semiconductor packaging and assembly. One such application has been the deposition of adhesive coatings onto the backside of silicon wafers....
Fuel Cell Production Revs Up. The Paste Printing Platform And Process Has Other Uses, Too.
Dec 18, 2008 | Clive Ashmore, Global Applied Process Engineering Manager; DEK.
Unless you've been living under a rock the past several years, you are no doubt keenly aware of the global drive toward alternative energy sources. Certainly this initiative is attractive because of the clear environmental benefits of developing fossil fuel substitutes, but also because of potential economic benefit. Although fuel cell technology has been proven viable for various applications, the production costs still remain relatively high, and further process development to promote low-cost, high-volume manufacturing is required to reach a price point that encourages widespread consumer acceptance....
Lean, Mean Dual-Lane Machines
Dec 27, 2007 | DEK
The latest screen printing platforms unlock more of the potential from dual-lane processing. Simultaneous demands to enhance flexibility while increasing utilisation and overall throughput apply to manufacturers operating at virtually any point in the mix-volume continuum: capacity must work hard to deliver the required return. As these lean manufacturing principles hold sway from the US and Europe to the Far East, no modern assembler has a second to spare....
A New Stencil Rulebook for Wafer Level Solder Ball Placement using High Accuracy Screen Printing
Dec 13, 2007 | Steve Watkin, Semicon Packaging Technologies Division, and Tom Falcon, Future Technologies Group, DEK
Printer-hosted processes for solder ball placement are now widely used for package technologies ranging from BGAs using ball diameters above 750μm to the latest WL-CSPs demanding 250μm diameter. This broadening spectrum of applications brings more choices in terms of stencil design rules and production methodologies....